What are the effects of casting and forging on metal properties for Farm machinery parts?
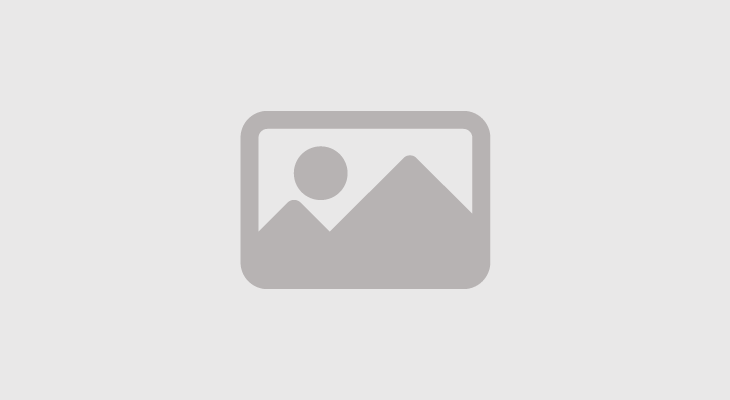
What are the effects of casting and forging on metal properties for Farm machinery parts?
Effects of Casting and Forging on Metal Properties for Farm Machinery Parts
Whether you are purchasing a new farm machinery piece, or looking for a way to enhance the durability and strength of your current parts, you need to know the effects of casting and forging on metal properties. This article will help you understand the differences between the two, as well as give you some tips on how to choose the best method for your needs.
Casting vs forging
Compared to casting, forging provides more strength, better wear resistance, and longer service life. In addition, forging provides a tighter grain structure.
Forging produces parts that are durable, have great impact properties, and are uniform in size. Castings, on the other hand, have less strength and wear resistance, and are not uniform in size of carbon steel.
In addition, forging may be more expensive than casting. In order to determine the best method for your project, you must narrow your priorities down. You also need to consider the cost of the materials and the amount of machining required to produce the final product.
Generally, castings are cheaper. In addition, they can be mass-produced and allow for large components. They also eliminate the need for a melting step.
In addition, castings can be made with many different metals. Forging, on the other hand, can only be used with a limited number of alloys. These are alloys composed of two or more chemical elements.
image source: https://www.pinterest.ph
Strength vs durability
Whether it is a casting or forging, a metal's strength and durability is important. This is because agricultural machinery needs sturdy components for their equipments. Cast iron and steel are popular metals. Each has different uses.
A casting is a molten metal poured into a mold. Typically, a casting is lighter than a forging. Castings are used for large and complex components that may have internal cavities. They are also cheaper than a forging.
A forging is a pounding process that produces a metal product with superior strength and durability. It involves a series of steps, including hammering, cooling steel in water or oil, pressing, and aligning the grain. These steps are repeated for each forging.
A forging is more accurate than a casting. Forgings have finer grain sizes. These grain sizes are crucial to the strength and durability of the forged product. A metallurgist can alter the grain flow in a forging, which is useful for improving metallurgical properties of precision metal parts.
Cost vs quality
Whether casting or forging is right for your farm machinery parts, it's important to consider both the cost and quality of the parts you are manufacturing. Forging and casting are both popular metal forming processes. Each process is effective for different projects and has its own benefits. It's important to choose the process that's right for your project.
If you have an intricate part that requires special mechanical properties, casting is the better choice. Castings are made with approved heat treatment methods and are strong, versatile and durable. They're also cheaper. Castings can be made from a variety of materials, including steel, copper, aluminum and magnesium.
Forging has an added advantage over casting because it's a physical process that physically forces the metal into shape. It's a high-volume manufacturing process, which means you can save on time and materials. Forging also has an important advantage over casting because it can eliminate defects in the cast workpiece.
image source: https://www.pinterest.ph
Aluminum forging
Whether you're looking for aluminum forging or other metal parts, the process used in the manufacturing process can affect the properties of the resulting product. A wide variety of methods are used to produce forgings and castings. These processes vary in terms of the temperature used, the types of metals used, and the type of processing equipment used.
Aluminum forgings are produced through controlled flow of material into a desired shape. It enables the design of forged parts that offer high strength-to-weight ratios and a uniform composition. It also provides the necessary toughness to allow the material to withstand higher impact loads.
Forging can also be used to create a variety of shapes, especially parts with internal passages. This can increase the range of economical forging shapes, and improve precision. The design of the forgings includes machining allowances. These allowances vary depending on the size and shape of the part.
Aluminum forging can be divided into two types: ambient forging and hot forging of alloy steel. The former is used for parts with close tolerances, while the latter is used for reducing section thickness in parts design.
Tags
Comment / Reply From
You May Also Like
Popular Posts
Newsletter
Subscribe to our mailing list to get the new updates!
Categories
- Places and Regions (349)
- Health & Science (3559)
- Jobs (188)
- Work Life (286)
- Opinions (426)
- Real estate & Properties (121)
- Shipping & Logistics (64)
- Sex & Relationships (1755)
- Movies & Animation (6102)
- Comedy (229)
- Travel and Events (427)
- Gaming (1185)
- History and Facts (1296)
- People and Nations (1020)
- Science and Technology (3704)
- Arts & Entertainment (1810)
- Life Style (3627)
- Education (3386)
- Economics and Trade (1950)
- Others (5396)
- News and Politics (3218)
- Cars and Vehicles (430)
- Pets and Animals (326)
- Digital Marketing & Web Develpment (4)
- Robotics, VR & AR (0)
- DFTUntoldStories (1)
- Celebrities (83)
- Mobile Solutions & Apps (0)
- Ecommerce & Clean Tech (0)
- Artificial Inteligence & IoT (0)
- Big Data & Cyber Security (0)
- Business (1780)
- Palscity Show (0)
- Sports Show (0)
- Politics & Leadership Show (0)
- Digitally Fit Show (0)
- Entertainment & Lifestyle Show (0)
- Business Show (1)
- In The Morning Show (0)
- DFT Reels & Shorts (0)
- Natural & Food (1141)
- People and Culture (11)
- Sports (1906)
- Fashion (116)
- Gossip (55)
- Music (116)